Joint Sealants vs Joint Fillers: Understanding the Difference
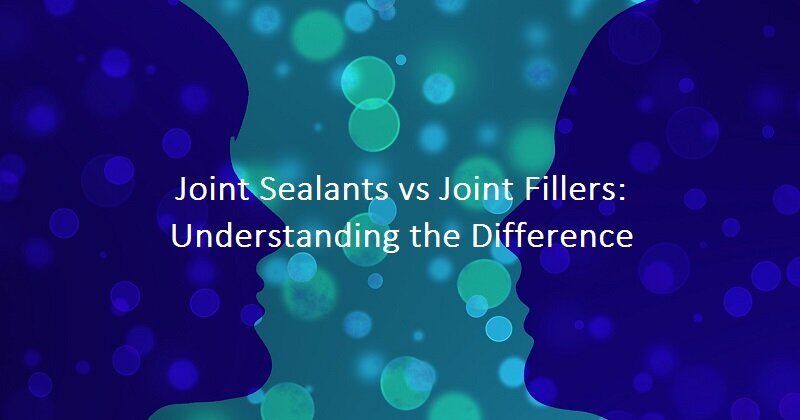
Last updated on September 28th, 2022
Joint sealants vs joint fillers: What is the difference?
Joint sealants and joint fillers are two different materials in terms of chemical composition, properties, function, installation, and applications.
Sealants
Modern joint sealants can be made of various materials including polysulfide, polyurethane, and silicone. Mainly, they are characterized by their ability to stretch and compress during the movement cycles of concrete joints. In fact, these elastomeric sealants can be of different types, grades, classes, and uses, according to ASTM C920. Besides, the main function of joint sealants, as their name implies, is to seal joints. Thus, they serve in preventing the intrusion of water and incompressible materials.
Joint sealants mostly occupy a depth less than that of the joint, in order to meet certain shape factor requirements. For example, the ideal shape factor is usually 1:2 (depth to width) for field-molded sealants. This mostly yields a depth less than that of the joint in most cases. Thereby, back up materials such as backer rods are generally needed to support the sealant when necessary. Besides, joint sealants are common in different types of joints, including construction, contraction, expansion, and isolation joints.
Joint fillers
Joint fillers are mainly of two types, epoxy and polyurea. And, unlike sealants, they are relatively semi-rigid materials which do not owe the same flexibility as sealants. Thereby, they can only accommodate to slight movements. In addition, their main function is to provide support and protect the joint edges, as well as to prevent the intrusion of incompressible materials and water to some extent.
Moreover, unlike sealants, semi-rigid joint fillers are only suitable for joints with little to no movements. For example, contraction joints generally exhibit less movements after most of the shrinkage occurs. And, if such joints require filling, a joint filler should occupy the full depth of the saw cut or groove.
The evolution of semi-rigid joint fillers
After the technological leap with elastomeric joint sealants, in particular polyurethanes in the 1960’s, they became very common in concrete joints. However, in applications where hard-wheeled vehicles were present, the edges of the joints suffered from significant spalling failures. This is mainly due to the fact that elastomeric joint sealants are flexible, and deflect under loading. Hence, the small hard wheels of trolleys and pallet jacks exerted impact and point loads to the edges of the joints, causing spalling.
Consequently, the industry switched back to filling control joints with rigid epoxy to provide edge protection. However, this practice welded the panels, and basically limited the effectiveness of such joints. Thus, this practice caused random cracking in the adjoining panels.
Based on this, a sealant contractor named Steve Metzger came up with the concept of semi-rigid joint fillers for industrial floors. His main aim was to develop a product which:
- Can bear the concentrated and point loads: This aims in providing support and protecting the joint edges from getting exposed to impact loads.
- Be able to accommodate to slight movements: Which allows the joint filler to stretch and compress during the slight movement cycles of the joint.
- And not form a strong bond with the walls of the joint: Unlike basic rigid epoxy, semi-rigid joint filler do not “weld” the slab panels to each other. Instead, under excessive stresses, the filler fails adhesively or cohesively instead of transferring these stresses to the adjoining panels.
Thereby, after extensive testing, he introduced an epoxy semi-rigid joint filler, in 1978, with a shore A hardness of 80. Since then, epoxy semi-rigid joint fillers evolved with higher shore A hardness and better flexibility, and semi-rigid polyureas joined.
Joint sealants vs joint fillers: A different crucial factor for each
When dealing with joint sealants, the shape factor can be an essential consideration for a satisfactory performance. In fact, a proper shape factor can reduce stresses and strains during the movement cycles of joints.
Whereas, with joint fillers, the shape factor is disregarded since the material is not as flexible as a sealant to accommodate for considerable movements, and should occupy the full depth of the saw cut or groove to provide support.
However, the crucial factor in the installation of semi-rigid joint fillers is timing. It is important to note that timing is also important with sealants, but not as much as with fillers. To illustrate, joint fillers are semi-rigid, and can only accommodate to slight movements, otherwise they will separate. Thereby, it is important to minimize the stresses or movements in order to achieve a satisfactory performance.
Consequently, one of the most effective factors to minimize the stresses in the filler is proper timing. Basically, contraction joints serve the purpose of controlling the location of cracks and relieving the shrinkage-induced stresses. And as concrete shrinks, these joints continue to open. But, most of the shrinkage occurs in the first four years, with the most critical in the first year, specifically in the first 90 days, according to ACI 302.1. Thereby, the longer you wait before applying the joint filler, the less stresses it would exhibit.