Failure Modes of Joint Sealants and How to Avoid Them
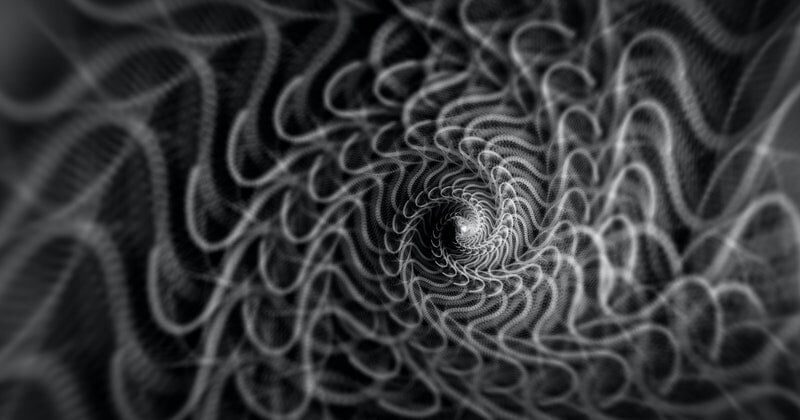
Last updated on July 12th, 2022
In order to better apprehend the failure modes of concrete joint sealants, specifically field-molded, we will first address their functioning mechanisms.
The functioning mechanism of field molded concrete joint sealants
In general, these sealants function through adhering to the sides of the joint, and by being able to accommodate to any movements. Thereby, as the joint opens, the sealant stretches, and exhibits strains in addition to stresses at its adhesion planes. Whereas, as the joint closes, the sealant compresses, and also exhibits strains, in addition to relatively lower stresses at its contact planes. In fact, during these cycles, the volume of the sealant remains constant, but its shape changes.
The failure modes of joint sealants
Concrete joint sealants can fail in many ways due to various reasons. In this section, we will briefly address the common failure modes of different types of sealants, their possible cause, and how to avoid them.
1. Adhesion failure of joint sealants
An adhesion failure is basically a partial or total loss of bond at the interface between the sealant and the side of the joint. In fact, this interface mostly exhibits tensile stresses (except in compression seals). However, when the stresses at the interface exceed the bond strength capacity, an adhesion failure occurs. Thereby, the main causes for an adhesion failure of joint sealants are related to: low bond strength or high stresses at the interface.
a. Low bond strength
In general, the main cause of a low bond strength is improper surface preparation. For example, the presence of debris, loose materials, oil, or contaminants, in addition to ignoring the surface roughness requirements or the application of primers when necessary, can significantly lower the bond strength of a sealant.
b. High stresses at the interface
Whereas, the main causes of high stresses at the interface mainly include inadequate sealant properties, inadequate shape factor, and bad sealant system configuration. These issues can cause a partial adhesion failure, such as peeling at points of stress concentration, or even a total adhesion failure. However, it is important to note that a partial failure can usually lead to an accelerated total failure. In addition, other causes may include hot tire pickup, such as on driveways, where a hot tire can cause additional stresses or even the extrusion of the sealant.
Solutions
- Proper surface preparation to increase bond strength: The surface should have an acceptable moisture content and temperature, and should be clean from any contaminants that can negatively affect the bond of the sealant. In addition, some sealant products may require surface roughening.
- Adequate sealant properties: An important relation to consider is that as the modulus of elasticity of the sealant increases, it strains less under the same stresses, and vice versa. Hence, a sealant with high modulus of elasticity exhibits higher stresses at its interface. However, it is important to note that a low modulus of elasticity is not always preferred, depending on the type of the joint and its exposure conditions.
- Adequate shape factor: It is important to consider a proper shape factor in order to avoid additional stresses at the interface. For example, a relatively deep application of the sealant with respect to its width can cause higher stresses at points of stress concentration. In general, a shape factor of 1:2 (depth to width) is preferred.
- Proper sealant system configuration: It is important to apply a system which does not induce additional stresses and strains to the sealant material. For example, a three-point adhesion system induces undesired stresses which can cause various failures, including adhesion.
2. Cohesion failure of joint sealants
A cohesion failure is the loss in the integrity of the sealant itself. In fact, this failure mode mostly occurs under tension, where the stresses in the sealant exceed its bearing capacity. Hence, the main causes behind a cohesion failure are mainly related to: inadequate choice of sealant or problems and factors that can negatively affect the performance of the sealant.
a. Inadequate choice of sealant
One of the main reasons for a cohesion failure of a concrete joint sealant is the inadequate choice of sealant. For example, a sealant that simply cannot accommodate to the movements of the joint can cause such failures. To illustrate, if a joint is expected to have a 25% movement, and the joint sealant is capable of only 12%, then a cohesion failure is likely to occur. Another example is an inadequate sealant which largely loses its flexibility as the temperature drops, which can also cause such failures.
b. Problems and factors that can negatively affect the performance of the sealant
In addition, there are various problems and factors that can weaken the sealant and cause cohesion failures. For example, problems include intrusion, punctures, improper shape factor, and improper sealing system configuration.
i. Intrusion
Intrusion is basically the entrapment of debris or other foreign materials in the sealant. In fact, intrusion can occur due to punctures, inadequate type of sealant (e.g. softening under high temperatures), or the combined effect of high tension strain and traffic. Thereby, a pocket of foreign materials forms in the sealant, which can generally lead to a cohesion failure.
ii. Punctures
Punctures are small holes that form due to variety of reasons such as excessive point loads or sharp objects. This problem creates weak spots, which can continuously progress under extension and movement cycles. Eventually, this can cause a cohesion failure of the sealant. In addition, punctures facilitate the intrusion of foreign materials, as we mentioned in the previous section.
iii. Improper shape factor
An improper shape factor can be defined as a depth to width ratio which is not suitable for a given joint. For example, a joint sealant that is too deep with respect to its width will exhibit higher strains than a less deep but wider sealant in a joint with considerable movements. In brief, an improper shape factor can cause high strains, which can lead to a cohesion failure.
iv. Improper sealing system configuration
An improper sealing system configuration includes for example a three-plane sealant system instead of two. This system generally introduces additional stresses to the sealant which causing cohesion or even adhesion failures.
Solutions
- Choose the right type of joint sealant: The sealant should have sufficient movement capacity with respect to the joint movement, resistant to punctures and abrasion, and applicable for the service temperatures.
- Use an adequate shape factor: It is important to use a proper shape factor, which reduces strains in the sealant.
- Follow a proper sealing system configuration: For example, it is important to use bond breakers or backing rods to avoid three-plane adhesion systems, thus avoiding additional undesired stresses.
3. Extrusion failure of joint sealants
An extrusion failure mode is the pullout of the sealant off its original place with flattening to one side. In fact, an extrusion failure mode of the joint sealant can occur mainly due to the combined effect of compression and traffic. Other causes include the combined effect of inadequate joint sealant and hot tire pickup, and sealant recovery issues.
i. Combined effect of compression and traffic
The combined effect of compression and traffic is one of the most common causes of extrusion failure in concrete joint sealants. In general, this failure mode occurs in applications where vehicle traffic is present, such as highways or even driveways. To illustrate, as the joint closes, it compresses the sealant, which can bulge above the surface. Thereby, at this stage, the traffic wheels can cause flattening of the extruded sealant along their direction.
Solutions
- Properly design the joints: The design includes various factors such as the spacing and number of joints. For example, decreasing the space between joints can help in reducing the extent of movements, and thus reduce the strains especially under compression, which is the controlling factor here.
- Use an adequate shape factor: For example, reducing the shape factor can reduce the strains, or the “bulging” of the sealant under compression.
- Select the right sealant: The sealant should also be applicable for the service and exposure temperatures. In addition, it should have high recovery.
4. Recovery failure of joint sealants
A recovery failure is the loss of the ability of the joint sealant to retain back to its shape during the movement cycles of the joint. In fact, a recovery failure mode can occur due to various causes including inadequate sealant type, exposure conditions, and aging.
For example, using a sealer which does not have high recovery and movement capacity on a joint with considerable movements and cycles can cause a recovery failure. Also, the exposure to weathering conditions, chemicals, temperature, and loads can sometimes cause the sealant to lose its ability to recover, depending on its type and quality. In addition, aging can influence the overall performance of the sealant, including its recovery, especially after its expected service life.
Solutions
- Choose the right type of sealant: The sealant should have a high recovery, and be suitable for the application, type of joint, and exposure conditions.
5. Other joint sealant failures
Other concrete joint sealant failures mainly include those that are related to appearance. In fact, an appearance failure mode of a joint sealant is the change in its intended or expected appearance, which can also affect its performance. Some examples include bloom, staining, change in color or discoloration, organic growths, and chalking.
Installation temperature is a crucial factor to consider
Temperature is an important factor when applying a sealant or sealing system for movement joints. Mainly, as the temperature rises, the movement joint closes, and as the temperature drops, it opens. However, it is important to mention that it is not about the air temperature, but the temperature of the members on the sides of the joint.
Based on the temperature’s effect, applying the sealant in the wrong conditions can cause additional stresses and strains, which can lead to failures. For example, applying the joint sealant during low temperatures, when the joint is open, would cause additional high stresses when the joint closes. Whereas, applying the joint sealant during high temperatures (which cause the joint to close), would induce additional tensile stresses as the joint opens.
Hence, it is important to apply the sealant during the “neutral” state of the joint. In fact, it can be determined by considering the mean temperature, or the mean joint opening width. Thereby, this practice can minimize the stresses in the sealant during the movement cycles of the joint.
Conclusion
There are various failure modes in concrete joint sealants including adhesion, cohesion, extrusion, recovery, appearance, and other failure modes. However, by following the best practices and choosing the adequate type of sealant, these failures can be avoided.