TOC-1: Self-Consolidating Concrete (SCC)
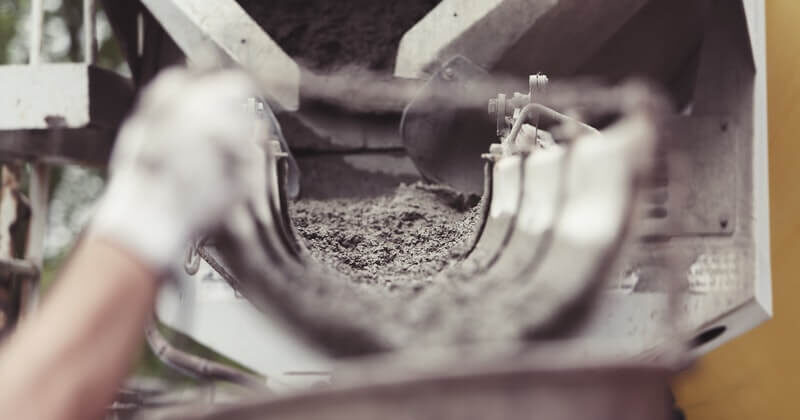
Last updated on January 1st, 2022
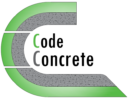
An Engineering Glance Types of Concrete
TOC-1: Self-Consolidating Concrete (SCC)
Code Concrete, March 26, 2021
Citing Information: Code Concrete (2021). TOC-1: Self-Consolidating Concrete (SCC). Online at: https://codeconcrete.com/toc-1-self-consolidating-concrete-scc/
Definition
Self consolidating concrete (SCC), also known as self compacting concrete, is a special type of concrete characterized by its high flowability. SCC has the ability to flow and spread under its own weight, while resisting segregation, and properly fill the mold and encase the steel reinforcements without the need for vibration or compaction.
History & Development
In the late 1980’s, a Japanese professor related the lack of durability and short service life of conventional concrete to improper consolidation, and established the concept of self consolidating concrete as a solution. Eventually, several state of the art reports, research papers, and guidelines on SCC were published. In 2004, a European group, with the cooperation with The UK Concrete Society, developed notable guidelines for the specification, production, and use of SCC. In 2007, the American Concrete Institute (ACI) presented an extensive guideline on self consolidating concrete.
Advantages & Disadvantages
Self consolidating concrete has many advantages compared to normal concrete in terms of overall cost, production, placement, performance, aesthetics, time, labor, equipment, and noise. These advantages are a result of the enhanced workability of SCC, specifically its high flowability and ability to consolidate without the need of external or internal vibration or compaction. However, achieving these unique characteristics comes with some disadvantages in terms of initial cost, paste volume, additional care on constituent materials, and plastic cracking. The main advantages and disadvantages of self consolidating concrete are shown in the following illustrations.

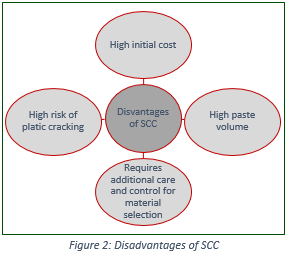
Applications
Following its real-scale successful application in Japan and the development of its guidelines, self consolidating concrete gradually began to be accepted and used in various applications worldwide. Usually, SCC is used in applications where: the reinforcement is dense or congested, the formwork is geometrically complex, or when the pumpability is a controlling factor. SCC has also been successfully used in infrastructure (tunnels, bridges, retaining walls, etc.), buildings, precast concrete elements, repairs, and architectural concrete members. Some of the interesting mega-projects that incorporated self compacting concrete include The One World Trade Center (where self compacting concrete with high compressive strength was used in the shear walls from the foundation to the 30th floor), Trump Tower (where about 3,500 cubic meters of SCC were continuously poured over a period of 22 hours), and Burj Khalifa (where different strength classes of self consolidating concrete were used in the piles, foundation, columns, and core walls).
Properties
The unique characteristics of self consolidating concrete are mainly related to its fresh properties rather than its hardened properties. The fresh required properties of SCC depend on various parameters including engineering properties, environmental conditions, placement method, quality control, constituent material properties and availability, structural detailing, formwork, cost, geometrical variables, finishing, and labor skill. The main fresh properties of self compacting concrete are usually expressed in terms of rheology (relating the shear stress and shear rate), or practical field requirements (evaluating the filling ability, passing ability, and stability of SCC). Typically, self consolidating concrete has slump flow values in the range between 450 and 760 mm, a passing ability on the L-box more than 0.8, and a column segregation less than 10%. SCC mixtures with T500 less than 2 seconds are considered to have low viscosity, whereas those with T500 greater than 5 seconds are considered to have high viscosity. In fact, evaluating the fresh properties for this type of concrete is essential , since SCC should not only have high flowability, but also sufficient stability to resist segregation.
On the other hand, the hardened properties are not considered to be a unique characteristic of SCC, and can be usually engineered through proper mix designing to meet the required specifications. However, it is important to mention four parameters that might be of a concern: modulus of elasticity, autogenous shrinkage, plastic shrinkage, and compression creep. Comparing SCC to conventional concrete with a similar compressive strength: SCC might show a reduction in the
modulus of elasticity, due to the increase in the sand to aggregate ratio. The autogenous shrinkage might be higher due to the lower water to binder ratio and higher content of cementitious materials. The plastic shrinkage might be of a concern due to the low surface bleeding. And the compression creep might be higher due to the higher paste volume.
Concerning aesthetics, self consolidating concrete shows enhanced surface appearance, with a reduction in surface flaws, blowholes, and honeycombing.
Test Methods
The uniqueness of self compacting concrete is in its fresh characteristics. Thereby, the main test methods to be discussed include the slump flow, T500, visual stability index, J-ring, L-box, and column segregation.
The slump flow is one of the common tests used to determine the filling ability of concrete without obstructions. A higher slump flow diameter means that concrete can spread farther and usually can fill a specific volume faster. A common standard test method to determine the slump flow of self consolidating concrete is ASTM C1611.
The visual stability index (VSI) test is used to evaluate the stability of self compacting concrete during the slump flow test. An indication value between 0 and 3 is given based on visual assessment. Lower values indicate stability whereas higher values indicate a segregation potential. However, VSI test is a visual test, and thereby its results may be subjective. This test is more of a quality control and is beneficial in comparing results from load to load, or when the concrete shows bleeding.
The T500 test is used to assess the viscosity of SCC. The result is the time in seconds for the slump flow to reach a diameter of 500 mm. The lower the value, the less viscous the mixture is, and the higher the value, the more viscous the mixture is.
The J-ring test is used to determine the passing ability of self consolidating concrete with the presence of obstructions. A higher J-ring flow diameter indicates that concrete can spread farther in the presence of obstacles such as steel reinforcements. The standard J-ring test method is ASTM C1621.
The L-box test is also used to determine the passing ability of SCC in the presence of obstructions. The result is the ratio of the height of concrete at the end of the box to height of concrete remaining in the vertical section. A value closer to 1.0 indicates a better passing ability.
The column segregation test is used to determine the segregation resistance of self compacting concrete. The result is the segregation percentage, comparing the weight of coarse aggregates in the bottom section to the upper section of a standardized cylindrical fresh concrete specimen. Lower values indicate less segregation. The standard column segregation test method is ASTM C1610.
Constituent Materials
Self consolidating concrete is mainly composed of cement, supplementary cementitious materials (SCMs), fine aggregate, coarse aggregate, admixtures, and water.
Cement should conform to international standards (such as ASTM C150, ASTM C595, ASTM C1157, or EN 197-1). Different types of cement may be required for different applications depending on several factors.
Supplementary cementitious materials (SCMs) should meet standard specifications (Silica fume/ASTM C1240 or EN 13263, Flyash/ASTM C618 or EN 450, Ground granulated blast furnace slag (GGBFs)/ASTM C989 or EN 15167, or other SCMs such as natural pozzolans, metakaolin, ground glass, etc…).
Fine aggregate and coarse aggregate should preferably conform to standard specifications as well. However, it may be acceptable to use aggregates that do not conform to standard specifications, as long as the required fresh and hardened properties of the mixture for the short term and long term are met. Different types of aggregates, in terms of density or composition, may be used for different applications. In addition, the absolute volume and the maximum particle size of coarse aggregate should be limited, based on several parameters.
Admixtures should also meet standard specifications. The essential admixture used in almost every self consolidating concrete is the high range water reducing admixture (HRWRA), which should conform to ASTM C494 or EN 934-2. Viscosity modifying admixtures (VMA) may also be used to improve the segregation resistance of SCC. Other admixtures such as set accelerators, set retarders, air-entrainers, and shrinkage reducers, may be incorporated similarly as in conventional concrete. Different types, brands, and dosages of individual admixtures may be required for different applications, and not all products or brands have the same performance.
Water to binder ratio in self compacting concrete is usually less than that of conventional concrete, and should meet similar standard specifications.
Other materials such fillers, fiber reinforcements, pigments, are also used in SCC.
Applied Principles
The key principles to achieve the unique fresh characteristics of SCC are briefly discussed. Some or all of these concepts are usually applied in the design of high-quality self consolidating concrete:
– Balancing the fluidity and viscosity of the paste through material selection and proper proportioning.
– Limiting the water to powder ratio.
– Incorporating supplementary cementitious materials to control several parameters, due to their effect on strength development, durability, fresh properties, heat of hydration, carbon footprint, cement content, etc… .
– Using a relatively high paste volume, which is responsible for mobilizing the aggregates.
– Controlling and evaluating the minimum required paste volume and excess paste volume.
– Limiting the total volume and maximum particle size of the coarse aggregate.
– Controlling the sand to aggregate ratio.
– Controlling the gradation or particle size distribution of constituent materials.
– Using inert fine materials to optimize the gradation when necessary.
Mix Proportioning
ACI 237 shows a basic mix design method used to estimate the required batch weights for trial SCC mixtures. The steps in this procedure can be briefly summarized in the following illustration.
The first step starts with determining the slump flow requirements, based on a given table. The second step is to select and proportion the coarse aggregate, taking into account the effect of reinforcement spacing, aggregate shape and texture, and particle size distribution on the volume and nominal maximum particle size of coarse aggregates. This procedure separates coarse aggregates into two categories, the first having nominal maximum particle size greater than or equals 12.5 mm, and the second having nominal maximum particle size less than 12.5 mm. In the case of the former category, the content of the coarse aggregate is calculated based on having its bulk volume, based on dry-rodded bulk density, as fifty percent of the volume of concrete. The combination of aggregates can be performed based on the 0.45 power chart. In the case of the latter category, taking equal volumes of coarse and fine aggregates is considered reasonable for the initial trial mixture. The third step is to estimate the powder and water contents, in which powder includes binder, inert fillers, and crushed materials with particles size less than 0.125 mm. The powder content can be estimated at the high range between 386 and 475 kg/m3 as a starting point for the trial mixture. The initial water content can be estimated based on the water to cement ratio and compressive strength relationship presented in ACI 211.1. The fourth step is to determine the paste and mortar volume, where paste includes powder, water, admixtures, and air; and mortar includes paste and fine aggregates. The paste volume and mortar volume are commonly in the range of 0.34 to 0.40 and 0.60 to 0.70, respectively. Following the fourth step, the admixtures are selected, then trial batches and laboratory tests are performed. Then the proportions are adjusted based on the test results in order to achieve the desired properties.
The common parameters for trial mix proportions based on this method are summarized in the following table.
During the development and extensive research on self-consolidating concrete, several mix design approaches and methods were used. The main mixture design methods can be categorized as follows:
– Empirical methods: they are based on objective and quantitative observations. In other words, they rely on experimentation and on the collection of data from previous experience. The earliest method used in the initial development of SCC in Japan was empirical. Several modified empirical methods were used later in the development of SCC mixtures. Empirical methods are used to determine the preliminary mix proportions, and then modifications are made based on trials and tests. These methods are considered to be simple, yet may be time-consuming due the required intensive testing.
– Statistical factorial methods: they are based on mathematical relationships, derived from factorial experiments, which correlate different proportioning key parameters to certain fresh and/or hardened properties. These relationships aim to establish a rational range of values for different parameters, based on the targeted properties, to consider for mix proportioning. These methods are considered beneficial since they cover a range of experimental conditions. However, complex relationships and variations in the properties of constituent materials may require intensive testing.
– Strength-based methods: they are based on the concept of determining the contents of different constituent materials based on a targeted compressive strength. Several methods were developed, and presented a structured and clear procedure to design SCC. These methods usually require less trial mixtures than the previously mentioned methods.
– Paste rheology methods: these methods are based on achieving certain paste rheology parameters to design SCC. Several methods were developed, in which some considered additional parameters including volumetric ratios of constituents, aggregate spacing, gradations, equivalent diameter of steel fibers, etc…. These methods are beneficial in evaluating the “theoretical quality” of SCC mixtures, and can help in reducing the number of trial mixtures.
– Particle packing methods: these methods are based on the concept of densely-packing particles through the optimization of the particle size distribution. Several methods were developed following different particle packing models. These methods are considered promising in designing self compacting concrete mixtures with low binder content, and usually require less trial mixtures and testing.
Technical Tips
– Increasing the thixotropy of SCC reduces the pressure on the formwork.
– Proper testing and good specification are essential components for successful application of SCC.
– Testing the modulus of elasticity, creep, and shrinkage of self consolidating concrete is important.
– Using a proper release agent is a key to achieve smooth finish in contact areas.
– Proper curing is essential in reducing the plastic shrinkage cracking of self compacting concrete.
References
– ACI Committee 237, “237R-07 Self-Consolidating Concrete,” Farmington Hills, 2007. |
– H. Okamura and K. Ozawa, “Mix-design for self-compacting concrete,” Concrete Library of JSCE, vol. 25, pp. 107-120., 1995. |
– P. S.W., “Self-Consolidating Concrete (SCC): Today’s Challenge and Tomorrow’s Prosperity,” in 5th North American Conference on the Design and Use of Self-Consolidating Concrete, Chicago, 2013. |
– G. F. Kheder and R. S. Al Jadiri, “New Method for Proportioning Self-Consolidating Concrete Based on Compressive Strength Requirements,” ACI Materials Journal, vol. 107, no. 5, pp. 490-497, 2010. |
– Y. Edamatsu, N. Nishida and M. Ouchi, “A rational mix-design method for selfcompacting concrete considering interaction between coarse aggregate and mortar particles,” in Proceedings of the first international RILEM symposium on self-compacting concrete, Stockholm, 1999. |

Any reproduction or redistribution of part or all the content of this document is strictly prohibited. It is only allowed to use content from this document for personal and non-commercial use, with proper reference acknowledging the source of the material.
Code Concrete – All Rights Reserved – | https://codeconcrete.com/ |