Industrial Revolution and Manufacturing Methods of Cement
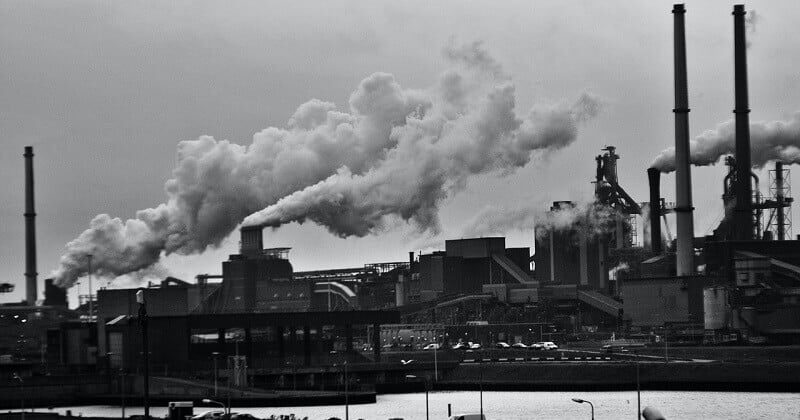
Last updated on February 7th, 2022
How is cement made?
After Joseph Aspden invented Portland cement in 1824, many developments in the manufacturing technique lead to modern Portland cement. Indeed, the main development was in 1845, when Isaac Johnson heated a mixture of chalk and clay at a much higher temperature than Aspdin did. Hence, this technique resulted in a more reactive and cementitious mixture. This is mainly due to the occurrence of clinkering and the formation of reactive minerals.
The three main developments in the production method of cement
After Johnson’s optimization, three essential developments in the production technique, in the twentieth century, further optimized the production process of modern Portland cement.
- First, the use of rotary kilns instead of vertical shaft kilns. This replacement improved the production efficiency and quality control.
- Second, the introduction of gypsum to the mixture constituents, which aids to control the setting time.
- And third, the introduction of ball mills which grind clinker to the desired size.
In brief, these developments set the foundation of the manufacturing method of modern Portland cement. In addition, this tailored the answer to how is cement made, when comparing early cement to modern Portland cement.
The typical manufacturing process of modern Portland cement
The following list summarizes how is cement made step by step:
- First Step: Quarrying the raw materials
- Second Step: Processing the raw materials
- Third Step 3: Producing the “raw mix”
- Fourth Step: Producing clinker
- Fifth Step: Cooling down the hot clinker
- Sixth Step: Producing the Portland cement
These six steps are essential in the production process of cement and define how is cement made.
Step 1: Quarrying the raw materials
The first step in the manufacturing process of Portland cement is to quarry the raw materials. Specifically, Portland cement’s raw materials primarily consist of calcium silicates, aluminates, and alumino-ferrites. These various raw materials are of calcareous, siliceous, aluminous, and ferriferous categories.
- Calcareous raw materials include limestone, marl, calcite, aragonite, shale, sea shells, cement kiln dust, chalk, and cement rock.
- Siliceous raw materials include clay, marl, flyash, shale, rice hull ash, sand, and slag.
- Aluminous raw materials include aluminum ore refuse, clay, flyash, bauxite, limestone, ore washings, slag, loess, and shale.
- Ferri-ferrous raw materials include ore washings, mill scale, shale, clay, iron ore, pyrite cinders, and blast-furnace flue dust.
Step 2: Processing the raw materials
After quarrying the raw materials, they are crushed, primarily screened, and stockpiled.
Step 3: Producing the “raw mix”
The third step is to prepare and mix the raw materials with specific sizes and proportions to obtain the “raw mix”. However, it is essential for this mix to have the adequate chemical and physical properties. Besides, the mixing operation can be either a dry or a wet method.
1. The dry method
On one hand, the dry method requires drying the raw materials till they reach a moisture content less than 1% before grinding. The drying process uses dryers, autogenous mills, air separators, or even the kiln’s hot exhaust gases. Afterwards, conveyors or bucket elevators transport the dried raw materials separately to their hoppers. Then, the materials are blended to form the raw mix. Finally, the raw mix is transported and stored in specific silos until it is fed to the kiln.
2. The wet method
On the other hand, the wet method requires adding water to the raw materials during grinding, thus producing a slurry. Then, pumps transfer the slurry to separate tanks, then to the precise mixing tanks, and finally to the storing tanks.
Dry vs wet method
By comparing both methods, the dry method requires less time and consumes less fuel than that of the wet method. However, the wet method produces better quality at a lower overall cost.
Step 4: Producing clinker
The fourth step is to place the raw mix in the pyro-processing system. This process transforms the raw mix into clinker. Clinker are hard-greyish spherical nodules with a diameter range of 0.15 to 0.52 centimeters. However, for this transformation to occur, the dry mix must pass through a long cylindrical inclined furnace, the rotary kiln. This high-temperature kiln typically has a diameter of 2.5 to 3 meters and a length of 90 to 120 meters. In addition, it is in-lined with refractory bricks. In fact, the rotary kiln is divided into three main zones, the drying, calcination, and clinkering zones.
Kiln: The drying zone
The first zone is the drying zone, which is the upper part of the inclined rotary kiln where the raw mix enters. In this zone, two processes occur to the raw mix, first the evaporation of water at 100°C, and second the dehydration at about 400°C.
Kiln: The calcination zone
The second zone is the the calcination zone, which is the central part of the kiln. The temperature of the calcination zone is about 1000°C. At this temperature, limestone decomposes into calcium oxide and carbon dioxide, producing a material in the form of nodules.
Equation 1: Decomposition of limestone during calcination
CaCO3 = CaO + CO2
Kiln: The clinkering zone
The third zone is the clinkering zone, which is the lower part of the inclined rotary kiln. The temperature of the clinkering zone is about 1500°C. At this temperature, lime and clay react to produce calcium silicate and calcium aluminate. Namely, lime or calcium oxide reacts with silicon dioxide to produce C2S (belite) and C3S (alite). Also, calcium oxide reacts with aluminum oxide to produce C3A. Additionally, calcium oxide reacts with aluminum oxide and ferric oxide to produce C4AF.
Equation 2: Formation of di-calcium silicate during clinkering
2CaO + SiO2 = Ca2SiO4 ….. (C2S)
Equation 3: Formation of tri-calcium silicate during clinkering
3CaO + SiO2 = Ca3SiO5 …. (C3S)
Equation 4: Formation of tri-calcium aluminate during clinkering
3CaO + Al2O3 = Ca3Al2O6 ….. (C3A)
Equation 5: Formation of tetra-calcium aluminoferrite during clinkering
4CaO + Al2O3 + Fe2O3 = Ca4Al2Fe2O10 ….. (C4AF)
Then These silicates and aluminates fuse to form hard-greyish spheres, clinker.
Step 5: Cooling down the hot clinker
The fifth step is to cool the freshly produced hot clinker. The cooling process uses reciprocating grates, planetary coolers, or rotary coolers. Hence, air cools down the clinker to a temperature of about 93°C. In fact, the air which passes through the cooling system to the rotary kiln also returns as combustion air, except for the reciprocating grate cooler which passes additional air.
Step 6: Producing the Portland cement
The final step is to grind and blend the mixture, thus converting clinker into Portland cement. Hence, ball mills or tube mills grind the clinker into fine powder. Then, during the final grinding, powdered gypsum is added to control the setting time of the final product, Portland cement.
Conclusion
The manufacturing method of cement has significantly evolved from the early cements to the modern Portland cement. However, the main principal remains the same – heating a mixture of well proportioned materials of specific chemical compositions.
Joseph Aspdin first created Portland cement in 1824. Then, Isaac Johnson optimized the manufacturing method mainly by increasing the temperature, which resulted in a more reactive product. Eventually, three main developments in the production process set the foundation of the manufacturing method of modern Portland cement, and redefined how is cement made.
Bibliography
- Gad, E. A. (2018). The Cement Manufacturing Process.
- Rahman, F. U. (2019, December 4). Manufacture of Cement- Materials and Manufacturing Process of Portland Cement. Retrieved from The Constructor Civil Engineering Home: https://theconstructor.org/building/manufacture-of-cement/13709/
- US EPA, E. F. (2011, May 18). Portland Cement Manufacturing.
- Winter, N. Cement History. Retrieved from Understanding Cement: https://www.understanding-cement.com/history.html