Types of Resin Floors
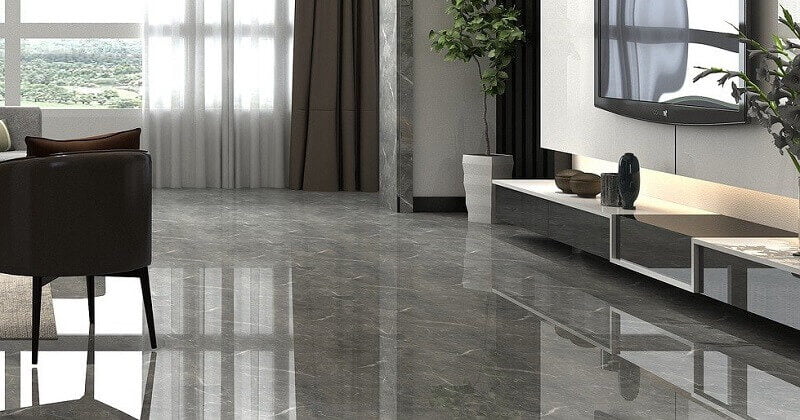
Last updated on July 17th, 2025
What is resin?
Resins resemble a viscous liquid or a solid material, either natural or synthetic, which can be transformed into a polymer. And since the topic is related to floors, we will be focusing on resins of synthetic origin.
Synthetic resins are manmade resins, which can be transformed into polymers by curing. These resins are popular in many applications including arts, jewelry, flooring, electronics, adhesives, and others. Besides, almost everyone is familiar with this material in a way or another, much like art resin, casting resin, floor resin, or AB glue.
However, although these products fall under the same broad category, the main difference between them may not only be in the intended use, but also in the material or type of resin.
Types of synthetic resin for floors
In general, there are many different types of synthetic resins, such as epoxy, polyurethane, acrylic, polyaspartic, polyurea, methacrylate, and others. Some of these resins are available as 1 part which cures when exposed to air either due to oxidization or due to moisture in the air, and some as 2 parts which cure when mixed together, where these parts consist of a resin and a curing agent. In fact, different types of resins have different physical, mechanical, and durability properties.
Understanding resin floors: resin sealing, coating, and flooring, are they the same?
Many people use the terms sealing, coating, and flooring interchangeably. But is this technically correct? Basically, it depends. Different codes and standards refer to synthetic resin protective toppings or floorings in a different terminology.
But in this guide, we will address this subtopic by referring to the (BS 8204-6) code of practice. This code classifies different types of resin floorings, in a technical and practical manner, into eight main types, under three main categories. Hence, it can be said that there are major technical differences between these terms. Basically, the main physical distinctions lie in the thickness and surface finish.
What is resin sealing?
Resin sealing is a two or more layers of resin, which have a total thickness less than 150 micrometers. The (BS 8204-6) code of practice mentions the term “seal” in Type 1 of its classification of resin floors.
Floor seal
A floor seal is typically less than 150 micrometers thick, and generally consists of two or more coats of a solvent or water-based sealer.
Sealers can be mainly categorized into two groups, penetrating and topical/film-forming. The former includes different types of water-repellents, water and oil-repellents, and surface hardeners and densifiers. Whereas the latter mainly includes acrylic, polyurethane, epoxy, and others. In fact, these types of sealers have different properties and overall performance.
You can read more about the best sealers for different applications in the following article, “Which Concrete Sealers are Best for Patios, Driveways, Pool Decks, and Garages“.
You can also learn how to choose the best sealer for your project in the following article, “How to Choose the Best Sealers for Concrete Floors“.
The general application procedure of a floor seal is as follows:
- First, prepare the surface.
- Second, apply a primer (depending on the type of sealer and particular product).
- Third, apply the first coat of the floor sealer.
- Fourth, apply the second coat of the floor sealer, generally when the first is tack-free or within the permissible time according to the specific product used.
A floor seal is generally suitable for light duty floors. The main benefit of a topical floor seal is that it provides some degree of protection against infrequent spills and some mild chemicals. In addition, it can enhance the colors and the overall appearance of the surface. Furthermore, it eases up cleaning when compared to bare concrete. However, floor seals typically have low slip resistance, but can be enhanced using a slip resistant additive.
What is resin coating?
Resin coating is two or more layers of resin, and is 150 to 1,000 micrometers thick in total. The (BS 8204-6) code of practice mentions the term “coating” in 2 types, Type 2 and Type 3, according to its classification of resin floors.
Types of resin coatings
The two types of resin coatings are floor coating and high build floor coating. These two types differ in thickness and overall performance.
Floor coating
This type of coatings has a thickness between 150 and 300 micrometers, and generally consists of two or more coats of a high-solids or solvent free resin.
The typical application procedure of a floor coating is as follows:
- First, prepare the surface.
- Second, apply a primer.
- Third, apply the first coat of the floor coating.
- Fourth, apply the second coat of the floor coating, generally when the first is tack-free or within the permissible time according to the specific product used.
A resin floor coating is typically used in light to medium duty floors. Briefly, it is somehow similar to a topical floor seal but thicker, can last longer, and provide a higher degree of protection and durability.
High build floor coating
This type of coatings has a thickness between 300 and 1,000 micrometers, and generally consists of two or more coats of a solvent free resin.
The general step by step application procedure of a high build floor coating is as follows:
- First, prepare the surface.
- Second, apply a primer.
- Third, apply the first coat of the floor coating.
- Fourth, apply the second coat of the floor coating, generally when the first is tack-free or within the permissible time according to the specific product used.
A high-build resin floor coating is typically suitable for medium duty floors. Compared to regular floor coating, this system is thicker, more durable and resistant, and thus can last longer. Mainly, it provides good resistance to infrequent spills and some chemicals, and has slight resistance to impact damage.
What is resin flooring?
Resin flooring is a synthetic resin layer or multiple layers, which have a thickness ranging from two millimeters to more than six millimeters. The (BS 8204-6) code of practice uses the term “flooring” in 5 of the types of synthetic resin floors, Type 4 to Type 8. These types can be categorized under the general term of resin flooring, and they can differ in thickness and surface finish.
Types of resin flooring
The five types of resin flooring include multi-layer, flow applied, resin screed, heavy duty flowable, and heavy duty resin. These types are different in thickness, surface finish, and durability.
Multi-layer flooring
This type of flooring is at least 2 millimeters thick, and typically consists of two or more layers of floor coatings (Type 2 or Type 3) or flow-applied flooring (Type 5), which confine a layer of aggregates. Hence, they are also known as sandwich systems.
The general step by step procedure of installing a multi-layer resin flooring is as follows:
- First, prepare the surface.
- Second, apply a primer.
- Third, apply the first coat of the floor coating or flow-applied flooring.
- Fourth, scatter the aggregates to the fresh first coat.
- Fifth, apply the second coat of the floor coating or flow-applied flooring.
- Sixth, you can apply a protective coating depending on the type of resin and exposure conditions.
A multi-layer resin flooring is generally suitable for medium to heavy duty floors. This system improves the resistance to wear, impact, and various chemicals. Its appearance and surface texture depend on the color of the resin, application methods, and on the type, size, and quantity of aggregates. In addition, its slip resistance is also related to the surface texture, but in general it is highly slip resistant.
Flow-applied flooring
Flow-applied resin flooring has a thickness between 1 and 3 millimeters, and is characterized by its self-levelling properties.
The basic procedure of installing a flow-applied flooring is as follows:
- First, prepare the surface.
- Second, apply a primer.
- Third, apply the self-levelling flooring resin coat. You can use a notched trowel or a notched squeegee to uniformly spread the resin, then roll over a spiked roller to avoid air bubble issues and give a smoother finish. Also, you can add an aggregate dressing to this system.
- Fourth, you can apply a protective coating, depending on the type of resin and exposure conditions.
A flow-applied resin flooring is typically used for medium to heavy duty floors. This system has a good resistance to wear and impact, and a very good resistance to chemicals. In addition, its appearance can vary from solid colors to multi-colors with different sheen levels. And the surface texture is generally smooth, but can be relatively roughened with aggregate dressings. However, its slip resistance is generally low, but can enhanced with an aggregate dressing.
Screed flooring
Screed resin flooring is generally at least 4 millimeters thick, and consists of a mixed material or heavily filled resin, and a sealing or surface coating.
The typical step by step installation procedure of a screed resin flooring is as follows:
- First, prepare the surface.
- Second, apply a primer.
- Third, apply the screed flooring mixed material. You can use a trowel to uniformly spread the screed, then finish with a steel trowel.
- Fourth, you can apply a coat or two of a compatible sealing or coating layer, using a roller or a squeegee.
A screed resin flooring is generally also suitable for medium to heavy duty floors. Mainly, it has a moderate resistance to impact but a low resistance to chemicals. Also, its surface texture can be smooth or lightly textured, with a slip resistance that depends on the sealing or coating finish, but typically has moderate slip resistance.
Heavy duty flowable flooring
This type of resin floors is generally at least 4 to 6 millimeters thick. It consists of a flowable resin containing aggregates. The major difference between heavy duty flowable flooring and flow-applied flooring is in the thickness and the incorporation of aggregates in the resin in the former.
The general step by step procedure of installing a heavy duty flowable flooring is as follows:
- First, prepare the surface.
- Second apply a primer.
- Third, apply the aggregate filled resin material. You can use a notched trowel or notched squeegee to uniformly spread the material, then roll with a spiked roller. You can also add an aggregate dressing to this system.
- Fourth, you can apply a protective coating, depending on the type of resin and exposure conditions.
A heavy-duty flow-applied resin flooring is suitable for heavy to very heavy duty floors. It is somewhat similar to the regular flow-applied flooring, but is thicker, more resistant, and highly durable. This system has an excellent resistance impact, and a very good resistance to various chemicals.
Heavy duty screed flooring
Heavy duty screed flooring has a thickness of at least 6 millimeters, and consists of a mixed material or aggregate filled resin. The main difference between this type of resin floors and screed flooring is that it is thicker, and is non-porous throughout its thickness.
The general procedure for installing a heavy duty screed resin flooring is as follows:
- First, prepare the surface to a suitable profile using the proper method.
- Second apply a primer.
- Third, apply the aggregate filled resin. You can use a trowel to spread the screed, and finish with a steel trowel.
A heavy-duty screed resin flooring is typically suitable for very heavy duty floors. Mainly, it is somewhat similar to the regular screed flooring, but is much thicker, resistant, and durable. It has excellent resistance to impact and to various chemicals. In addition, its colors and texture generally resemble a textured matt “speckled uniform finish”, which is highly slip-resistant.
Summary of the characteristics of the different types of resin floors
The following table sums up some of the typical characteristics and properties of floor seals, coatings, and flooring, based on (BS 8204-6) code of practice. You can find much more details by referring to the aforementioned code.
How to choose which type of resin floors is best for a certain application?
Selecting the ideal type of resin floors requires considering numerous factors, with a long checklist of major parameters. In this section, we will address the three major factors, the site requirements, preferences and customizations, and product characteristics.
Site requirements
In order to determine the requirements of a certain application, there are several parameters that should be considered. These mainly include the loading conditions, exposure conditions, and others.
Loading conditions
The loading conditions play a major role in the selection of the ideal type of resin floors for a particular application. For instance, the type of traffic (such as pedestrians, normal vehicles, industrial vehicles, heavy vehicles, etc.), their frequency, and the type of load (including static or dynamic, impact) can determine the duty level of the floor. In fact, this is a crucial factor since different types of resin floors are suitable for different duty levels. For example, as previously mentioned, a floor seal is suitable for light duty, which includes light foot traffic and occasional normal vehicles.
Exposure conditions
Exposure conditions mainly include the exposure to chemicals, temperature, and weathering conditions. In fact, this is a huge topic and is beyond the scope of this article, however we will briefly and concisely address its major parameters.
The exposure to chemicals is one of the main causes of stains, discolorations, reduced durability, and even local failure of resin floors. Thereby, selecting the adequate type of resin for floors and the type of resin floors, being resistant to the particular chemicals of concern is crucial. In fact, the chemical resistance varies between different types of resin floors, but what is more significant is the type of resin or its chemical composition. The ACI 515.2R provides vital information about the selection of the adequate protective treatment based on the chemical exposure.
In addition, the temperature exposure conditions can also affect the selection of the ideal type of resin floors. It is important to take into account the ambient temperature, the temperature of chemicals and spillage, the exposure to direct heat/flames or hot objects, and the cleaning temperature. Also, it is important to consider the duration of such exposure conditions.
Furthermore, the exposure to weathering conditions is also a controlling factor. In fact, the exposure to direct sunlight or ultraviolet (UV) radiations is one of the main parameters here. For example, epoxies are generally sensitive to UV radiations and can start yellowing with frequent exposure and time. Whereas, polyurethanes are usually UV resistant.
Others
Other parameters that should be considered when determining the site requirements include hygiene, slip resistance, and anti-static properties. For example, the hygiene requirements can affect the method and temperature of cleaning and the surface texture. Also, the slip resistance requirements can influence the texture and surface smoothness. Accordingly, these parameters, in addition to the anti-static requirements, can directly affect the selection of the type of resin and the type of resin floors.
Preferences and customizations
The preferences and customizations are also an important factor to consider. These mainly include the color, level of sheen or gloss, texture, and other customizations.
Mainly, these parameters are all related to aesthetics. And not all types of resins or resin floors provide similar colors, level of gloss, texture, and customizations.
In general, most types of resin for floors are available in a wide range of colors, and different levels of sheen. However, the texture preferences are usually limited based on the type of the resin floor. For example, a floor seal can generally provide little to no change to an existing texture of a concrete floor, depending on the type of the sealer. Besides, the texture is also related to the slip resistance, and is not solely an aesthetic parameter.
In addition, multiple colors and accent colors are customizations that are available with some types of resin and resin floors, and are generally only for aesthetic purposes. Furthermore, color flakes are also a customization option that is available with some types of resin floors, which can alter the appearance of the floor or both its appearance and texture.
Product characteristics
The characteristics and properties of the product or system is yet another important factor to consider. Mainly, these include the expected lifespan, cost, installation and curing time, environmental impact, thickness, aesthetics, and overall performance.
Industrial vs residential resin floors
In general, the requirements of industrial resin floors are much more different than those of residential resin floors. This is mainly because the loading conditions, exposure conditions, hygiene, slip resistance, and anti-static properties are more controlling in the former. For this reason, the types of resin floors that are usually suitable for these applications are different.
Residential resin floors
Residential resin floors are often subjected to occasional to regular foot traffic and occasional vehicles of rubber tires (such as a garage floor). Thereby, they usually range from light to medium duty. Also, they are limitedly exposed to certain chemicals, spillage, or high temperatures, and can have slip resistance and hygiene requirements (such as a kitchen floor). Hence, type 1 and type 2 are often the choice for residential resin floors. Besides, type 3 is also popular for a relatively long lasting and durable solution for garage floors.
Industrial resin floors
Industrial resin floors are often subjected to constant foot traffic, industrial vehicles (such as forklifts, trolleys, trucks, or heavily loaded vehicles), point loads, and/or impact loads. Hence, they often range from medium to very heavy duty. In addition, they are also often more exposed to chemicals, spillage, or high temperatures. Furthermore, they are more likely to have specific hygiene, slip resistance, and/or anti-static requirements. Thereby, type 4 to type 8 are usually the most popular choice for industrial resin floors. However, other types are also suitable for lighter industrial conditions.
Conclusion
There are different types of resin for floors (such as epoxy, polyurethane, methacrylate, and many others), which have different chemical compositions, and provide different overall performance and durability. In addition, there are eight different types of resin floors, based on the followed code of practice, which also have different overall performance and durability, and mainly vary, physical wise, in their thickness and surface texture. But in order to select the ideal type for a particular application, it is important to consider three main factors, the site requirements, preferences and customizations, and product characteristics, with the numerous parameters of each.
Bibliography
- ACI Committee. (2013). ACI 515-2R-13 Guide to Selecting Protective Treatments for Concrete.
- BS Committee. (2008). Screeds, Bases and in Situ Floorings – Synthetic Resin Floorings. BS 8204-6 Code of Practice.
- (1997). Specification & Guidelines for Synthetic Resin Flooring. Surrey: European Federation of National Trade Associations.
- (2018). Guide to the Specification and Application of Synthetic Resin Flooring. The Resin Flooring Association.
- (2021). Guide to the Selection of Synthetic Resin Flooring. The Resin Flooring Association.
- ICRI Committee. (2013). ICRI 310.2R Selecting and Specifying Concrete Surface Preparation for Sealers, Coatings, Polymer Overlays, and Concrete Repair. International Concrete Repair Institute.